This review studied various hydrocarbon decomposition
methods reported in the literature for reducing automotive CO2
emissions as part of carbon management. The ‘value-added’ carbon
economy reduces H2 costs and motivates H2 economy progress.
The objective of hydrocarbon decomposition is to eliminate or
drastically reduce the amount of CO2 emitted from primary fuel
resources. A wide variety of decomposition methods and
techniques have been reported in the literature for the generation
of carbon-free H2 from gaseous or liquid hydrocarbon fuels [1].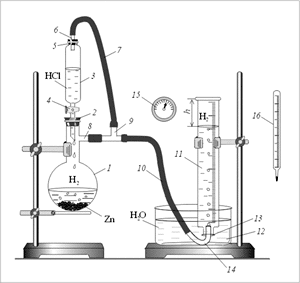
There is steadily increasing awareness of the need to reduce CO2
emissions to limit global warming. Many scientists now believe
that an increase in the concentration of CO2 and other green house
gas (GHG) such as methane and nitrous oxide, will increase the
mean global temperature of the earth. In general, CO2 comprises
85–95% of the total GHG emissions. Transportation is certainly the
sector that has the largest potential impact for reducing GHG
emissions. Motor vehicles are a major source of CO2. Globally,
transport related emissions of CO2 are growing rapidly accounting
for 20–25% of the CO2 release in the atmosphere [2].
Fuel consumption and CO2 emission of a vehicle are two
indissociable parameters. According to the U.S. Environmental
Protection Agency (EPA) estimates [3], the average annual amount
of CO2 emitted by a passenger car is about 4.6 ton (equivalent to 1.3
ton of elemental carbon) assuming a total annual consumption of
about 2000 l of gasoline. In other words, the combustion of one
gallon of conventional gasoline produces about 8.9 kg of CO2 and
the average car CO2 emission is about 230 g/km. Table 1 presents
the emission rates for hydrocarbons, CO, CO2, oxides of nitrogen
(NOx) and particulate matter. The calculations for ‘annual emission’
and ‘fuel consumption’ were based on an average annual mileage of
20,000 km (12,500 miles) and a fuel economy of 10 km/l or 23.8
miles per gallon (mpg). These emission factors and fuel consumption
rates are for gasoline-fuelled passenger cars and light-duty
trucks only.
methods reported in the literature for reducing automotive CO2
emissions as part of carbon management. The ‘value-added’ carbon
economy reduces H2 costs and motivates H2 economy progress.
The objective of hydrocarbon decomposition is to eliminate or
drastically reduce the amount of CO2 emitted from primary fuel
resources. A wide variety of decomposition methods and
techniques have been reported in the literature for the generation
of carbon-free H2 from gaseous or liquid hydrocarbon fuels [1].
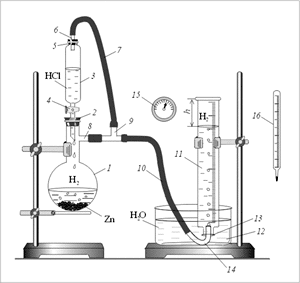
There is steadily increasing awareness of the need to reduce CO2
emissions to limit global warming. Many scientists now believe
that an increase in the concentration of CO2 and other green house
gas (GHG) such as methane and nitrous oxide, will increase the
mean global temperature of the earth. In general, CO2 comprises
85–95% of the total GHG emissions. Transportation is certainly the
sector that has the largest potential impact for reducing GHG
emissions. Motor vehicles are a major source of CO2. Globally,
transport related emissions of CO2 are growing rapidly accounting
for 20–25% of the CO2 release in the atmosphere [2].
Fuel consumption and CO2 emission of a vehicle are two
indissociable parameters. According to the U.S. Environmental
Protection Agency (EPA) estimates [3], the average annual amount
of CO2 emitted by a passenger car is about 4.6 ton (equivalent to 1.3
ton of elemental carbon) assuming a total annual consumption of
about 2000 l of gasoline. In other words, the combustion of one
gallon of conventional gasoline produces about 8.9 kg of CO2 and
the average car CO2 emission is about 230 g/km. Table 1 presents
the emission rates for hydrocarbons, CO, CO2, oxides of nitrogen
(NOx) and particulate matter. The calculations for ‘annual emission’
and ‘fuel consumption’ were based on an average annual mileage of
20,000 km (12,500 miles) and a fuel economy of 10 km/l or 23.8
miles per gallon (mpg). These emission factors and fuel consumption
rates are for gasoline-fuelled passenger cars and light-duty
trucks only.
2. Onboard hydrogen generation
The development of an onboard system capable of converting
liquid hydrocarbon fuels, such as gasoline, into a stream of H2-rich
gas and carbon would make it possible to power internal
combustion engine (ICE) vehicles using standard fuels with H2.
Capturing and storing carbon onboard the vehicle could help
mitigate climate change [4].
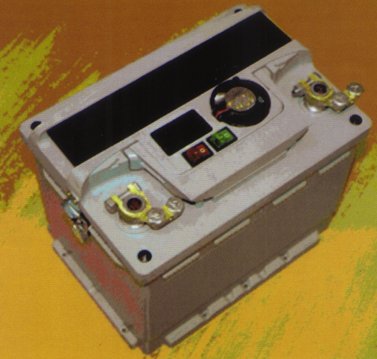
processing for H2 and carbon production is clear: the utilization of
conventional fuels at improved efficiency and lower pollution
levels. The advantage of using liquid hydrocarbons as a H2 storage
medium is that the current fuel distribution infrastructure can be
used for the transportation, storage, and dispersal of the liquid
hydrocarbon. Moreover, the development of fuel-efficient engines
that produce fewer pollutants has been a major objective for many
years. The response of engine manufacturers, oil refiners, academic
researchers and catalyst industries to this public policy pressure
has been remarkable [5]. A steady increase in fuel economy and a
decrease in unwanted emissions have been achieved. However, it
is now believed that a new approach to reduce CO2 emissions is
required.
that produce fewer pollutants has been a major objective for many
years. The response of engine manufacturers, oil refiners, academic
researchers and catalyst industries to this public policy pressure
has been remarkable [5]. A steady increase in fuel economy and a
decrease in unwanted emissions have been achieved. However, it
is now believed that a new approach to reduce CO2 emissions is
required.
2.1. Hydrogen generation by catalytic routes (SMR, POX and ATR)
Turning gasoline into H2-rich gas for automobiles has been the
object of much R&D. Jamal and Wyszynski [6] reviewed the use of
H2 and H2-enriched gasoline as a fuel for SI-engines and the
techniques used to generate H2 from liquid fuels such as gasoline
and methanol, onboard the vehicle. Processes such as thermal
decomposition, SMR, POX, and exhaust gas reforming were
discussed. The authors discussed onboard generation of H2 for
use as an alternative or supplemental fuel for spark ignition
engines. A considerable amount of both theoretical and experimental
work has been done in this field. Predictive and
experimental results of the various investigators were reviewed
and summarized. The authors claimed that the difficulty of
gasifying or handling the solid carbon makes hydrocarbon
decomposition not suitable for onboard H2 generation.
There are various strategies to provide H2 to the engine. If H2 is
stored onboard in a tank, the mixture will consist of pure H2 and
gasoline. If H2 is obtained by processing a certain fraction of
gasoline in an onboard POX reformer, two different reformer gases
can be obtained. The first has a typical composition (by volume):
21% H2, 24% CO and 55% N2 (ignoring trace components). Since
such reaction is exothermic, the lower heating value (LHV) of the
reformer gas is roughly 15% lower than that of the incoming
gasoline [7]. The second gas is obtained water-gas shift reaction
and has a typical composition of 45% H2, 20% CO2 and 35% N2.
Allgeier et al. [8] presented a brief comparison of the various
types of onboard reformers (Table 2). A storage for reformate gas is
needed to cover the time during the reformer is being warmed up
to its operation temperature and as a buffer during high dynamic
transients. A wide variety of processes are available for onboard H2
generation from gaseous or liquid fuels [9]. The three main
onboard processes differ according to the nature of the primary
fuel used (ammonia, methanol, ethanol, gaseous or liquid
hydrocarbons) and to the chemical reactions involved (decomposition,
steam reforming or POX). Onboard generation of H2 is
certainly feasible from a technical standpoint but it is far from
evident that it could simply replace pure H2, stored in compressed
tanks or liquefied. Trimm et al. [5] reviewed the onboard
conversion of methanol, methane, propane, and octane to H2. A
combination of oxidation and steam reforming (indirect POX) or
direct POX is the most promising processes for H2 fuel cell. Indirect
POX involves combustion of part of the fuel to produce sufficient
heat to drive the endothermic steam reforming reaction. Direct
POX is favored only at high temperatures and short residence times
but is highly selective. However, indirect partial oxidation is shown
to be the preferred process for all fuels.
Other researchers investigated the utilization of auto-thermal
reforming (ATR) of gasoline for onboard generation of H2 [10,11].
ATR has been widely accepted as the most promising route to meet
efficiency, weight and volume, durability, and cost goals for
onboard fuel processors for automotive fuel cell systems.
Reforming catalysts are being developed to meet the unique
operating requirements for reforming complex fuel mixtures, such
as gasoline. Huffman and co-workers [12] and Goodman and coworkers
[13] used dehydrogenation of liquid hydrocarbons (such
as cycloalkanes) to produce CO-free H2. The advantage of using
liquid hydrocarbons as a H2 storage medium is that the current
distribution infrastructure can be used for the transportation,
storage, and dispersal of the liquid hydrocarbon. Supportedbimetallic
catalysts based on Fe, Ni and Pt are among the most used
catalysts.
2.2. Hydrogen generation by plasma route
Several different plasma reactors have been developed by
different research groups for onboard H2 generation from gasoline
using POX and ATR. Only a few plasma reactors have however been
developed for SMR of hydrocarbons. Several researchers [14–18]
have developed a non-thermal plasma reactor based on gliding arc
technology for gasoline reforming. These technologies are claimed
to be the most relevant techniques for onboard H2 generation
suitable for a large range of fuel flow rate. The initial version of a 2-l
plasmatron device required as much as 2 kWof electrical energy to
operate. The unit was developed to use an average of less than
100 W. Early systems took many seconds to produce H2 from cold
exhaust, an important disadvantage in real-world use, as emissions
are highest at this time. The latest versions were running in less
than a second. Moreover, the first prototypes produced H2 at just
one flow rate, however, recent prototypes managed transient or
varying flow demands equally well [14].
2.3. Onboard hydrogen supplementation to gasoline
The concept of H2 supplementation to gasoline in SI-engines
relies on the improvement of the thermal efficiency of engines
using conventional hydrocarbon fuels by supplementing them
with relatively small quantities of H2. The addition of H2 to the
cylinder charge can extend the lean limit equivalence ratio while
maintaining a sufficiently high flame speed. This will eliminate the
need to treat NOx emissions altogether. In this way the main fuel is
used more efficiently and only a small quantity of H2 is needed.
Jamal and Wyszynski [6] concluded that the operation of the
engine with 5–10 wt.% of H2 fuel makes it possible to operate the
engine in the very lean regime, which would not have been
possible without the presence of H2. A small amount of H2 added to
the air intake of a gasoline engine would enhance the flame
velocity and thus permit the engine to operate with leaner air to
gasoline mixture than otherwise possible. Although combustion
engines are expected to remain the dominant form of propulsion
for the next 20–30 years, there will be a wider range of vehicle
technologies and fuel types to address the economic, social and
environmental challenges of increased mobility.
The introduction of H2 as a supplemental automotive fuel
could be hindered by serious logistic problems. Worldwide, no
distribution system exists for H2, and its storage as a highpressure
gas or cryogenic liquid requires vehicle capabilities
which do not exist commercially. These potential difficulties,
however, can be avoided by generating H2 in an onboard gas
generator using gasoline or other liquid hydrcarbons as feedstock.
Conte and Boulouchos [7] suggested that combustion of mixtures
of H2 and gasoline appears to be a good opportunity to join the
major advantages given by both fuels, avoiding many problems,
especially if small amounts of H2 are produced onboard directly
from gasoline. Use of H2 and gasoline blends seems to be
especially suitable for part load operation and reduction of
emissions during cold start. Some researchers have suggested that
a move toward a mix of transportation fuels and H2 may offer a
potential solution for reducing CO2 emissions. Because of the
lower carbon content of the fuel mix (gasoline and H2), it will be
possible to achieve carbon emission reduction. The technology of
usingH2 as a combustion enhancement in ICE has been researched
and proven for many years. The benefits are factual and well
documented.
Cohn [17] summarized the benefits of H2 addition as follows:
i. H2 addition provides a large increase in fuel octane number.
ii. High octane fuel allows higher performance engines (turbocharging,
high compression ratio).
iii. Engines can be smaller and more efficient.
iv. H2 addition also facilitates ultra-lean burn.
v. Engine efficiency can be increased by up to 30%.
Beister and Smaling [18] reported on the progress made with
the Hydrogen-Enhanced Combustion Engine (HECE) concept, as
applied to an SUV-class 3.2-l V6 test engine. The promise of HECE is
that the addition of a small amount of H2 to the cylinder charge can
allow homogeneous charge ultra-lean burn combustion engines to
operate much leaner than otherwise possible. Enhancing gasoline
combustion with a small H2 gas stream pointed toward a potential
estimated improvement in gasoline fuel economy of 20–30%,
depending upon the baseline engine.
In another application, Cohn [17] installed and tested the
plasmatron fuel converter on a commercial diesel car engine
thereby reducing NOx emissions by 80%. The goal of diesel
reformation by the plasmatron was the conversion of the heavy
diesel compounds into H2, CO, and light hydrocarbons for use in
after-treatment applications. The onboard H2 gas was used as a
low-cost, highly efficient, clean-burning, fast-starting regenerator
of particulate matter and NOx filters, which are used in diesel
exhaust gas after-treatment. For NOx catalyst regeneration
applications, the plasmatron may be turned on for a few seconds
every half minute or so. For diesel particulate filter applications,
the plasmatron could well be operated for a few minutes every few
hours resulting in much smaller duty cycles [15].
The addition of H2-rich gas to gasoline in an ICE seems to be
particularly suitable for achieving a near-zero emission Otto
engine, which would be able to easily meet the most stringent
regulations [7]. A bottled blend of CO, H2, and N2 (24%, 21%, 55% by
volume) was chosen to simulate the most likely output of a POX
reformer suitable for ICE applications. Experiments were carried
out on a Lombardini 4-stroke, 2-cylinder, 0.5-l engine, model LGW
523 OHC. The engine was equipped with a water-cooled EGR line
and water trap. Investigation on flame propagation was carried out
using ion-detection probes on the cylinder head surface and an
optical spark plug for light emission detection in the ignition
phase.
The results of measurements included fuel consumption,
engine efficiency, exhaust emissions, analysis of the heat release
rates and combustion duration, for both pure gasoline and blends
with H2-reformer gas. Simulations were performed to better
understand the engine behavior and NOx formation. The results
showed a significant decrease of unburned hydrocarbons (UHC)
and NOx emissions to near-zero. Light increase in CO emissions was
detected and CO2 emissions could be reduced by 3.5% in the FTP
cycle. Moreover, a significant increase of engine efficiency was
measured, which seems to be enough to compensate and
overcome the losses due to POX of gasoline in the onboard
reformer [7].
A conceptual design for the reduction of CO2 emissions from
transportation vehicles was proposed for producing hydrogen and
carbon using known hydrocarbon decomposition technology
onboard a vehicle. The produced hydrogen is then used in ICE
thus reducing CO2 emissions [4]. One of the advantages of the
proposed conceptual onboard fuel decomposition system is that
the vehicle will still be fuelled by liquid hydrocarbons (gasoline or
diesel), thus avoiding many of the direct infrastructure problems
associated with H2. Part of the gasoline (25 vol.%) is decomposed
onboard, and converted into H2 and carbon. H2 is then burned in
the engine and carbon is stored onboard for further sale, depending
on its quality. The decomposition of gasoline does not introduce
any energy losses since exhaust energy is used for the process.
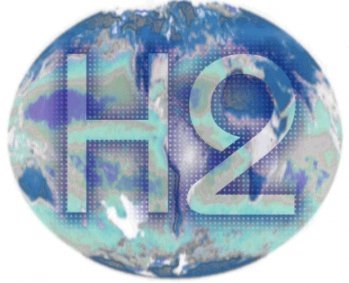
However, the onboard fuel decomposer and carbon storage may
introduce some weight penalty.
Allgeier et al. [8] reported on the advanced emission and fuel
economy concept by using combined injection of gasoline and H2
in SI-engines. The authors tested concept for an SI-engine
consisting of combined injection of gasoline and H2. An H2-
enriched gas mixture was injected additionally to gasoline into the
engine manifold. The gas composition represents the output of an
onboard gasoline reformer. The simulations and measurements
showed substantial improvements in the combustion process
resulting in reduced cold start and warm up emissions and
optimized part load operation. The replacement of gasoline by H2-
rich gas during engine start led to zero hydrocarbons in the exhaust
gas. The mixed fuel operation enabled high EGR rates up to 50% or
extended lean burn limits resulting in reduced pumping losses and
increased effective engine efficiency.